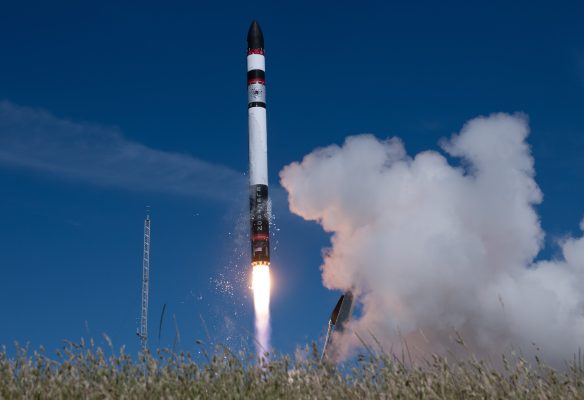
Rocket Lab is preparing for its next launch, currently set to take place in May from its launch facility in New Zealand. The payload for the flight are two satellites to join BlackSky’s Earth observation constellation, but Rocket Lab has a secondary goal crucial to its aim of adding reusability to its Electron launch vehicle: Recovering the booster stage after its return from space.
This isn’t the first time Rocket Lab has done a booster recovery; last December, it fished one out of the sea following its aptly-named ‘Return to Sender’ mission. For this flight, dubbed ‘Running Out of Toes,’ the goal is roughly the same, but the Electron vehicle has some upgrades and modifications that will help Rocket Lab gather even more data, and make progress towards actually fully reusing one of these boosters once they get it back.
“We were very, very pleased with the condition of the [first] booster we got back with basically no modifications to any of the thermal protection systems,” Rocket Lab CEO and founder Peter Beck explained in an interview. “The way that we enter with the booster is obviously engines-first and propagate a big shockwave forward. This next flight is the next iteration where we’ve upgraded the heat shield to be able to actually carry those loads, because we know those loads now.”
Flight one provided plenty of valuable data about what the actual stresses were on the Electron booster during re-entry — information that engineers on the ground could make educated guesses about, but couldn’t actually really know without a real-world test. The data collected by sensors onboard the rocket during that December flight provided Rocket Lab the ability to redesign Electron’s heat shield for a “major increase in performance and strength,” according to Beck.
This second flight will test the efficacy of those improvements, and provide even more data to the Rocket Lab team, which will be used to inform the design of the third and final planned recovery test. That will focus on adjusting the re-entry procedure so that the Electron booster sheds even more of its speed while coming back into the atmosphere, which makes Rocket Lab’s final recovery steps — a parachute-assisted slowdown and a mid-air helicopter capture — more viable.
“There’ll be one other design iteration after this, where we will look to scrub even more velocity in the air for more heat off the stage, to get us to that point where it really is worth introducing the other elements of the helicopter to go and pick up a stage that we feel like we could go and re-fly,” Beck said.
That third and final splashdown test should happen sometime later this year, if all goes to plan. And while Rocket Lab doesn’t aim to actually re-fly any of the boosters from these three development tests, Beck told me that certain components from the first booster they got back have been re-integrated into this second test vehicle, and the plan is to recover and re-use even more parts for test #3.
Beck said that bringing the booster back to the Rocket Lab factory and essentially cutting it into tiny pieces is actually the best way for the company’s engineers to learn about what happens during re-entry, and what parts of the rocket are affected most.
“There’s nothing like putting a stage back in the factory to really understand,” he explained. “You can have all the instrumentation you want, but we brought that stage back here and the first thing we did is, we cut it up. We cut all the heat-affected areas, all of the areas that are in the shadow of flow, and then start doing tensile polls on them to understand the material properties.”
All of this work drives towards the end goal of re-flying a recovered Electron booster — which will be a major accomplishment not only because it should help Rocket Lab increase its launch pace, but also because the vehicle was never designed for reusability to begin with. I asked Beck whether that first re-flight of a recovered Electron will be a commercial mission, or just a test without a customer payload.
“I would imagine it would be a commercial mission, simply because we’re not going to put anything on the pad that we don’t have really high confidence in anyway,” he said. “I suspect the first reused vehicles will have quite a lot of refurbishment on them, because if you look at the only other company that has demonstrated reusability [SpaceX], it’s been many, many years of learning and understanding. You don’t just kind of grab a launch vehicle, say it looks good, put it back on the pad and fly again. It’s a very iterative process of building confidence and assurance.”
While introducing reusability to Electron has benefits in its own right for that launch vehicle, the process of developing that capability has also been invaluable for Rocket Lab’s efforts to build out its next spacecraft, the higher-capacity Neutron launch system, according to Beck. Neutron is designed to launch and land propulsively, and to include a lot more usability by design from the very start.
“Electron was designed to be the world’s most manufacturable launch vehicle — Neutron is designed to be the most reusable launch vehicle,” Beck said. “They’re very different paradigms, but unusually we now have experience in both. For Neutron, the innovation really is around reusability, and there’ll be some interesting bits shortly, when we we reveal a little bit more about the vehicle architecture, that will make it very obvious to what degree we’re going to make this a reusable launch vehicle.”